Unlocking Spiral Freezer Potential: Strategies for Enhanced Performance
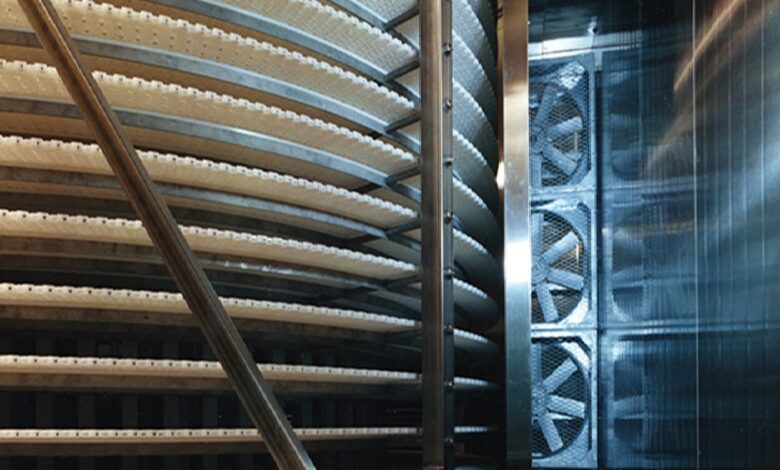
Spiral freezers are essential in the food processing industry, providing an efficient solution for rapidly freezing products while maintaining quality. To maximize the performance of these sophisticated systems, it is crucial to understand the key components and strategies that can enhance their efficiency and longevity. This article explores the importance of spiral freezer systems, the role of pressure gauges, and the best practices for optimizing these systems.
Understanding Spiral Freezer Systems
The Role of Spiral Freezer Systems
Spiral freezer systems are a vital component in the food processing chain, offering a continuous freezing process that preserves the quality and safety of various food products. Unlike traditional freezers, spiral freezers utilize a compact design, allowing large quantities of food to be frozen uniformly in a relatively small space. The spiral conveyor belts transport products through a low-temperature environment, ensuring even freezing and minimal product degradation.
These systems are particularly effective for freezing items such as bakery products, seafood, poultry, and prepared meals, where maintaining the structural integrity and appearance of the product is critical. The efficiency of a spiral freezer system directly impacts the throughput and overall productivity of a food processing facility, making it essential to implement strategies that enhance its performance.
Key Features and Benefits
Spiral freezers are known for their ability to handle high volumes of products, thanks to their compact design and efficient use of space. The spiral configuration allows for more product to be processed in less time compared to linear freezing systems. Additionally, spiral freezers provide consistent airflow and temperature distribution, which is crucial for maintaining the quality and texture of frozen products.
The automation capabilities of spiral freezer systems also contribute to their efficiency. Automated controls and monitoring systems help ensure optimal operating conditions, reducing the likelihood of human error and improving overall productivity. These systems can be tailored to the specific needs of the facility, providing flexibility in product handling and freezing parameters.
Optimizing Performance with Pressure Gauges
The Importance of Pressure Gauges in Spiral Freezers
Pressure gauges play a critical role in maintaining the optimal performance of spiral freezer systems. These instruments monitor the pressure levels within the refrigeration system, ensuring that the freezer operates within the required parameters. Accurate pressure readings are essential for maintaining the correct temperature and airflow, which are key to achieving uniform freezing and preventing product damage.
Pressure gauges also help in identifying potential issues before they escalate into major problems. For instance, abnormal pressure readings can indicate a refrigerant leak, compressor malfunction, or other issues that could compromise the performance of the freezer. By regularly monitoring pressure levels, operators can take proactive measures to address these issues, reducing downtime and maintenance costs.
Best Practices for Pressure Gauge Maintenance
To maximize the effectiveness of pressure gauges in spiral freezer systems, it is important to implement regular maintenance and calibration procedures. Regular calibration ensures that the gauges provide accurate readings, which is essential for maintaining the integrity of the freezing process. Inaccurate readings can lead to suboptimal freezing conditions, resulting in product spoilage and increased energy consumption.
It is also important to inspect pressure gauges for signs of wear and tear, such as cracks, leaks, or corrosion. Damaged gauges should be replaced immediately to prevent inaccurate readings and potential system failures. Additionally, operators should be trained to interpret pressure gauge readings correctly and to respond promptly to any anomalies.
Strategies for Enhanced Performance
Regular Maintenance and Cleaning
One of the most effective strategies for enhancing the performance of spiral freezer systems is regular maintenance and cleaning. Over time, ice buildup, debris, and other contaminants can accumulate on the freezer components, reducing efficiency and increasing energy consumption. Regular cleaning helps to prevent these issues, ensuring that the freezer operates at peak performance.
Maintenance procedures should also include checking the condition of conveyor belts, fans, and other moving parts. Worn or damaged components should be replaced promptly to avoid unexpected breakdowns and costly repairs. Additionally, regular inspection of the refrigeration system, including compressors, evaporators, and condensers, can help identify potential issues before they lead to system failures.
Energy Efficiency Optimization
Energy efficiency is a critical factor in the operation of spiral freezer systems, as it directly impacts operating costs and environmental sustainability. Implementing energy-saving measures, such as optimizing temperature settings and improving insulation, can significantly reduce energy consumption without compromising product quality.
Variable speed drives (VSDs) can be used to control the speed of fans and compressors, allowing for more precise temperature control and reducing energy usage during low-demand periods. Additionally, integrating energy management systems with spiral freezer controls can provide real-time data on energy consumption, enabling operators to make informed decisions about energy usage and identify opportunities for further optimization.
Training and Education
Finally, investing in the training and education of personnel is essential for maximizing the performance of spiral freezer systems. Operators should be well-versed in the principles of refrigeration, the specific requirements of the products being frozen, and the operation of the freezer system itself. Proper training ensures that operators can identify potential issues, make informed decisions about system settings, and perform routine maintenance tasks effectively.
Ongoing education and training programs can also help keep personnel up to date with the latest advancements in freezing technology and best practices. This knowledge can be applied to optimize system performance, reduce downtime, and improve overall efficiency.
Conclusion
Unlocking the full potential of spiral freezer systems requires a comprehensive approach that includes regular maintenance, accurate pressure gauge monitoring, and energy efficiency optimization. By implementing these strategies, food processing facilities can enhance the performance of their spiral freezers, ensuring consistent product quality, reducing operational costs, and extending the lifespan of their equipment.